
Carbon Footprint of the Dairy Industry: Challenges, Regulations, and Reduction Opportunities
Businesses across all sectors are facing increasing demands to reduce greenhouse gas emissions, with sustainability becoming the new standard. In the dairy industry, emissions span all three scopes of carbon accounting, with the largest share falling under Scope 3 indirect emissions. This article explores where these emissions originate, what reduction strategies are available, and what is essential for building an effective and realistic sustainability strategy.
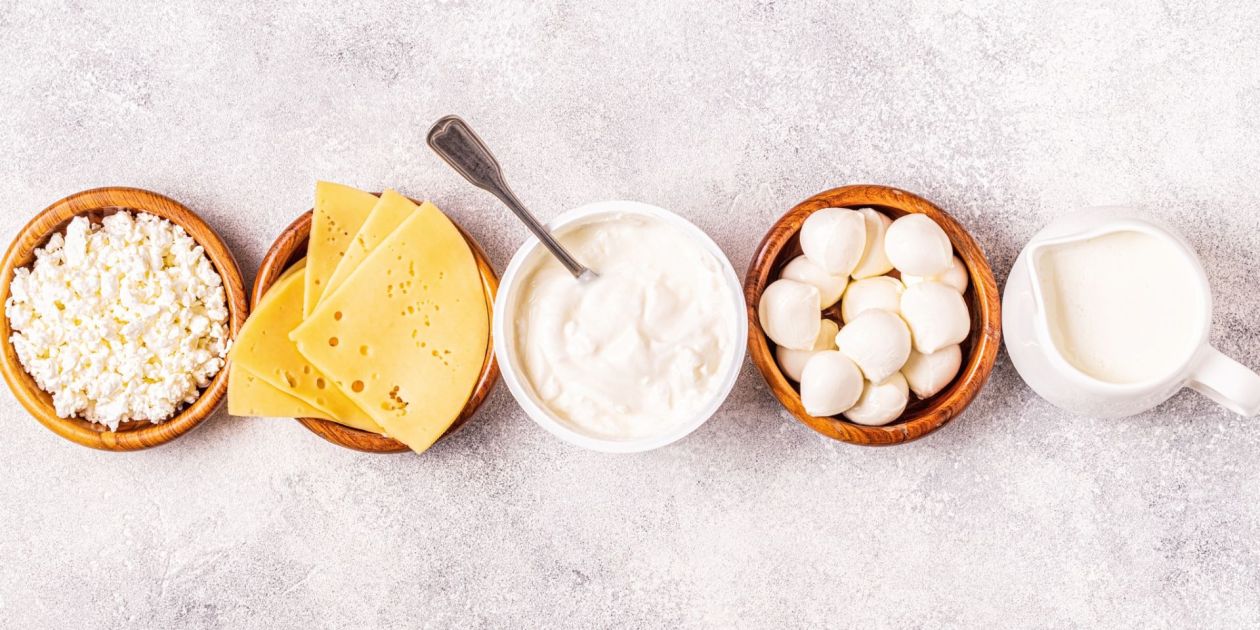
In recent years, the carbon footprint has become one of the key environmental indicators across many industries, including the food sector. The growing focus on sustainability, consumer pressure, and tightening legislation are pushing dairy companies to find ways to effectively calculate and reduce their greenhouse gas emissions.
Whatever the motivation may be, carbon accounting provides businesses with valuable insight into where emissions originate and what they can — or cannot — do about them. In this article, we’ll focus specifically on the carbon footprint in dairy processing companies.
Especially in the dairy industry, it’s crucial to recognize from the outset that the majority of emissions occur outside the company itself. Over 80% of the carbon footprint of a typical dairy processor stems from the production of raw materials, primarily the milk itself — in other words, from something the company does not directly control. That’s why it makes sense to consider the carbon footprint within the framework of the three Scopes of responsibility defined by the GHG Protocol: Scope 1 includes direct emissions, Scope 2 covers indirect emissions from purchased energy, and Scope 3 includes all other indirect emissions, such as those across the entire supply chain. Each scope presents different opportunities for influence, and a sustainable strategy must address each one specifically.
What You Actually Control: Operations and Energy
Scope 1 includes emissions that arise directly from the company’s own operations — for example, from burning natural gas, which is commonly used in dairies to heat milk, produce steam, or dry the product. The amount of natural gas used during drying depends on the type of product (e.g., composition, proportion of bound and free water) and the process applied (e.g., demineralization, vacuum evaporation, lactose crystallization, drum or spray drying)1.
If the company operates its own wastewater treatment plant, it may also be a significant source of methane. This potent greenhouse gas is primarily generated through anaerobic processes. Another category in this scope is refrigerants, though most facilities today use modern refrigerants with low environmental impact, and the risk of leakage no longer plays a major role as it did in the past.
Transport and logistics also fall under Scope 1 if the dairy operates its own vehicle fleet. However, transport and logistics typically account for less than 2% of the total carbon footprint of a dairy, making it an area with limited potential for major reductions — though optimising routes or using more efficient vehicles can still make a difference.
Scope 2 relates to indirect emissions generated during the production of electricity, heat, or steam that the dairy company purchases and uses for its operations. When it comes to electricity, the key factor is not just how much is used, but also what kind is being purchased. If it comes from a standard energy mix, the carbon footprint will reflect emissions from coal-fired and other fossil-fuel power plants. This makes it all the more important to consider the company’s energy consumption strategy.
A functional energy management system is fundamental for the sustainable implementation of any new innovations. Before investing in your own renewable energy sources, it makes more sense to first implement an effective energy management system, achieve maximum energy savings, and then begin purchasing verified green electricity — energy with certified origin that can be easily reflected in carbon accounting.
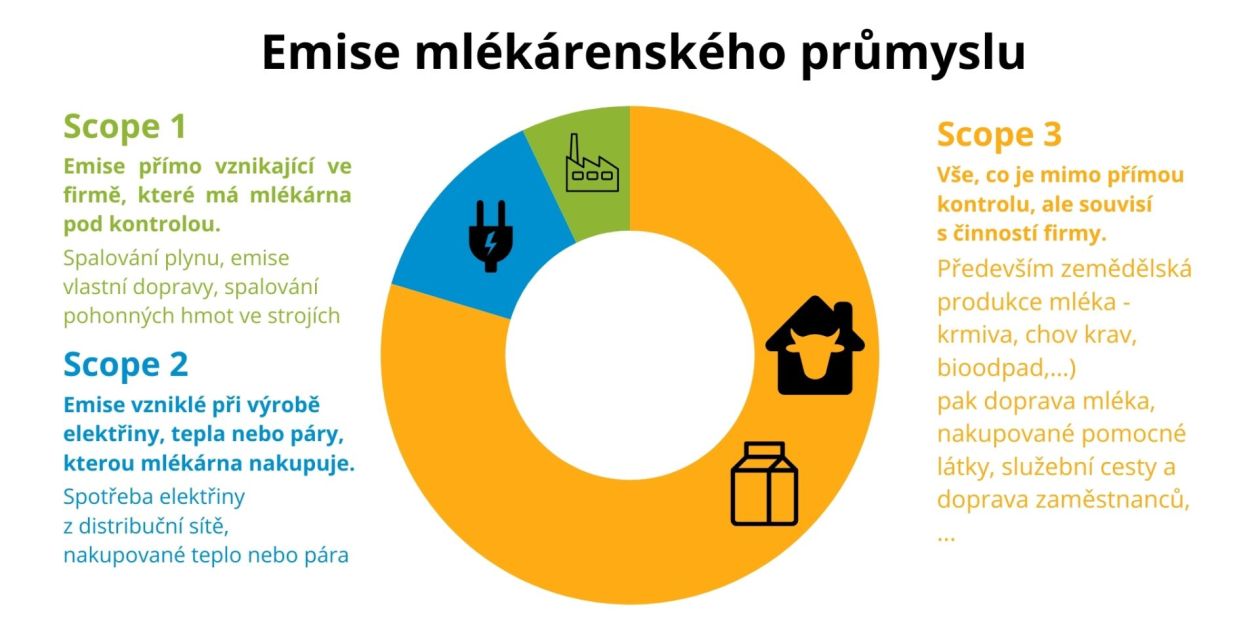
The Main Driver of the Carbon Footprint: Milk Production
The most complex — yet also the most significant — part of the dairy industry’s carbon footprint lies in Scope 3, which includes all other indirect emissions across the supply chain. In the case of dairy processing, one item clearly dominates: milk production. It is often responsible for more than three-quarters of a dairy company's total carbon footprint.
The main factor here is livestock farming itself. Cows are ruminants and during digestion they produce methane — a greenhouse gas approximately 28 times more potent than carbon dioxide2.
Methane, along with another significant gas, nitrous oxide, is also released in large quantities when handling manure. A promising solution may be switching to straw bedding, which produces solid manure instead of slurry — a more stable and less emission-intensive material — or constructing a biogas plant, where methane is intentionally produced from a mix of slurry and plant biomass. This methane is then combusted in a cogeneration unit, significantly reducing its release into the atmosphere while serving as a renewable energy source.
Feed composition also plays a key role — research shows that adding seaweed or fat-based supplements to the diet can significantly reduce methane production during digestion3.
Supplier selection, purchasing conditions, and especially long-term dialogue about sustainability are powerful tools. No change happens overnight — but stable relationships and a genuine effort to understand farmers’ real-world capabilities are essential for any transformation.
Beyond milk itself, Scope 3 also includes packaging materials. Polyethylene, aluminum, paper, and other packaging components not only require energy to produce but may also present an environmental burden at the end of their lifecycle. Some dairies are therefore transitioning to more sustainable alternatives, such as reusable glass bottles or recyclable packaging.
Scope 3 may also include external transport, the purchase of auxiliary substances (such as enzymes, cultures, or additives), fruit and other ingredients, employee commuting, business travel, waste processing… Yet compared to milk production itself, these factors usually have only a marginal impact on the company’s total carbon footprint.
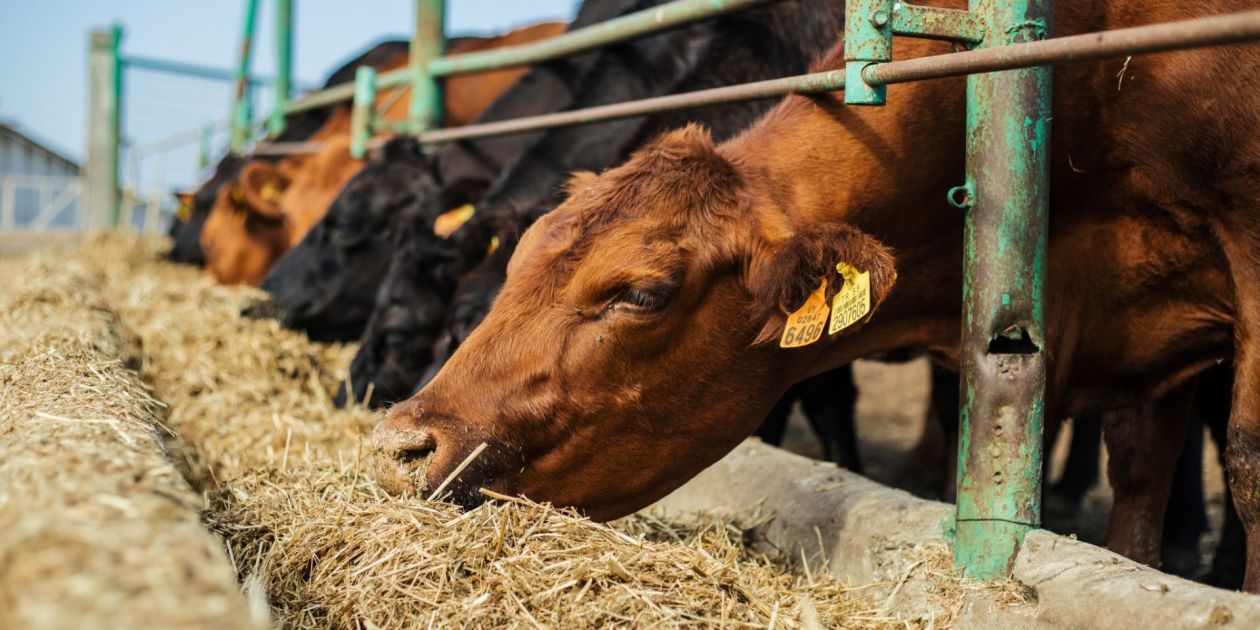
Opportunities for Reducing the Carbon Footprint in Dairy Production
Reducing the carbon footprint of dairy companies is a complex challenge that affects both operations and the entire supply chain. There is no one-size-fits-all solution — the path forward lies in a combination of technological innovation, more efficient production processes, sustainable investments, and, most importantly, building meaningful relationships with farmers and suppliers.
A good starting point is to focus on what the company can directly control: quality energy management, efficient use of drying and cooling technologies, and choosing more environmentally friendly packaging materials. In the long run, however, it is essential to also focus on what happens beyond the factory gates — with milk producers, whose practices will increasingly impact the success of dairy processors themselves.
This is where true competitiveness lies for the future. In a time of growing demand for sustainable products and increasing international pressure, this is no longer just about meeting obligations — emissions reduction is becoming a key survival strategy in the marketplace.